Рычаги нижние ВАЗ-2123. Каталог 2000г.
На складах : 1377 шт.
На складах : 2121 шт.
На складах : 343 шт.
На складах : 1440 шт.
На складах : 448 шт.
На складах : 154 шт.
На складах : 47 шт.
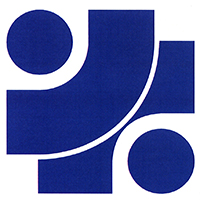
Производственное объединение «Трек» было основано в октябре 1995 года для выпуска комплектующих для легковых автомобилей. Основное направление деятельности ГРУППЫ «ТРЕК» — проектирование, производство и продажа элементов подвески, рулевого управления, трансмиссии, тормозной системы. Маркетинговые требования, переданные подразделениям НИОКР, трансформируются в новые инновационные изделия, проходящие все возможные виды проверок: компьютерное моделирование, стендовые и дорожные испытания. В новых конструкциях активно используются современные материалы, позволяющие нам предлагать нашим покупателям продукцию с улучшенными потребительскими свойствами по долговечности и надежности. Так, например, применение оригинальных решений при создании конструкции чехла ШРУС (наличие патента) и стойки стабилизатора, которые изготавливаются теперь из современных полимерных материалов, позволило создать изделие, по своим характеристикам значительно превышающее предыдущие аналоги. Не обделены вниманием и шарнирные соединения, конструкция которых постоянно совершенствуется. В результате покупатель получает инновационный продукт с улучшенными характеристиками. Процесс изготовления продукции включает в себя следующие виды производства: - прессовое – холодная и горячая объёмная штамповка, - механообрабатывающее – токарно-фрезерная группа оборудования, включая современные обрабатывающие центры EMAG, - переработки полимерных материалов – современное оборудование, в том числе термопласт–автоматы LG, - сборочное – с использованием высокопроизводительного специального оборудования, - инструментальное – с помощью современного обрабатывающего центра позволяет обеспечивать основное производство необходимым инструментом и оснасткой. Производственные мощности предприятия позволяют производить более миллиона шарнирных изделий в месяц. Контроль за качеством осуществляется на всех стадиях изготовления продукции (в том числе используется координатно-измерительная машина WENZEL). Система менеджмента качества предприятия сертифицирована на соответствие международному стандарту ISO 9001:2000 и национальному стандарту ГОСТ Р ИСО 9001:2001.
На складах : 40 шт.
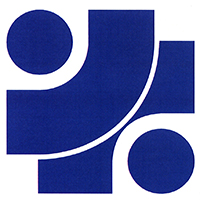
Производственное объединение «Трек» было основано в октябре 1995 года для выпуска комплектующих для легковых автомобилей. Основное направление деятельности ГРУППЫ «ТРЕК» — проектирование, производство и продажа элементов подвески, рулевого управления, трансмиссии, тормозной системы. Маркетинговые требования, переданные подразделениям НИОКР, трансформируются в новые инновационные изделия, проходящие все возможные виды проверок: компьютерное моделирование, стендовые и дорожные испытания. В новых конструкциях активно используются современные материалы, позволяющие нам предлагать нашим покупателям продукцию с улучшенными потребительскими свойствами по долговечности и надежности. Так, например, применение оригинальных решений при создании конструкции чехла ШРУС (наличие патента) и стойки стабилизатора, которые изготавливаются теперь из современных полимерных материалов, позволило создать изделие, по своим характеристикам значительно превышающее предыдущие аналоги. Не обделены вниманием и шарнирные соединения, конструкция которых постоянно совершенствуется. В результате покупатель получает инновационный продукт с улучшенными характеристиками. Процесс изготовления продукции включает в себя следующие виды производства: - прессовое – холодная и горячая объёмная штамповка, - механообрабатывающее – токарно-фрезерная группа оборудования, включая современные обрабатывающие центры EMAG, - переработки полимерных материалов – современное оборудование, в том числе термопласт–автоматы LG, - сборочное – с использованием высокопроизводительного специального оборудования, - инструментальное – с помощью современного обрабатывающего центра позволяет обеспечивать основное производство необходимым инструментом и оснасткой. Производственные мощности предприятия позволяют производить более миллиона шарнирных изделий в месяц. Контроль за качеством осуществляется на всех стадиях изготовления продукции (в том числе используется координатно-измерительная машина WENZEL). Система менеджмента качества предприятия сертифицирована на соответствие международному стандарту ISO 9001:2000 и национальному стандарту ГОСТ Р ИСО 9001:2001.
На складах : 20 шт.
На складах : 140 шт.
На складах : 179 шт.
На складах : 36 шт.
На складах : 11 шт.
На складах : 25 шт.
На складах : 22 шт.
На складах : 75 шт.
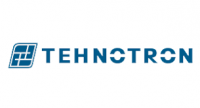
TEHNOTRON — созданное в Набережных Челнах передовое предприятие машиностроительной направленности, водящее в состав холдинга «ТЭМПО». Технотрон обеспечивает запчастями сферу коммерческой и сельскохозяйственной техники, в особенности электрооборудование, краны и почвообрабатывающую аппаратуру.
Располагая внушительной технической и научной базой в Набережных Челнах, Tehnotron независимо осуществляет полный цикл изготовления продукции, от проектирования и подготовки ресурсов, до тестирования и реализации товара, необходимого, в том числе для экономических нужд легкой и тяжелой промышленности.
Важно отметить, что в структурно-производственной цепи, есть место для проверки итогового продукта испытательным центром, который ответственен не только за предотвращение возможных проблем, но и за наиболее продуктивное совершенствование характеристик каждого конкретного изделия. Своим конкурентным преимуществом Технотрон выделяет особую технологию окрашивания автокомплектующих из SMC.
Бренд Tehnotron отвечает за соответствие высоким международным стандартам качества, что регулярно подтверждается обновляемым перечнем сертификатов и независимым органом оценки United Registrar of Systems Ltd. (URS Certification), благодаря контролю сырья, материалов и входящих комплектующих. Производственный потенциал в концерне позволяют конструировать и собирать все элементы самостоятельно в Набережных Челнах, не привлекая сторонние организации.
В настоящее время Технотрон в основном ориентированы на активное сотрудничество с такими автомобильными марками как ПАО «КАМАЗ», ОАО «МАЗ», «Группа ГАЗ», DAIMLER KAMAZ RUS и АЗ «УРАЛ». Компания стремится выйти на стабильный рост объемов производства, освоить также и региональные рынки и консолидировать автопромышленность.
Ассортимент:
- Система охлаждения
- Система питания
- Оперение кабины (экстерьер а/м 5490)
- Принадлежности кабины
- Элементы подвески
- Тягово-сцепные устройства
- Электрика
- Седельно-сцепные устройства
- Троллейный шинопровод и многое другое
На складах : 229 шт.
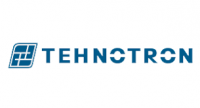
TEHNOTRON — созданное в Набережных Челнах передовое предприятие машиностроительной направленности, водящее в состав холдинга «ТЭМПО». Технотрон обеспечивает запчастями сферу коммерческой и сельскохозяйственной техники, в особенности электрооборудование, краны и почвообрабатывающую аппаратуру.
Располагая внушительной технической и научной базой в Набережных Челнах, Tehnotron независимо осуществляет полный цикл изготовления продукции, от проектирования и подготовки ресурсов, до тестирования и реализации товара, необходимого, в том числе для экономических нужд легкой и тяжелой промышленности.
Важно отметить, что в структурно-производственной цепи, есть место для проверки итогового продукта испытательным центром, который ответственен не только за предотвращение возможных проблем, но и за наиболее продуктивное совершенствование характеристик каждого конкретного изделия. Своим конкурентным преимуществом Технотрон выделяет особую технологию окрашивания автокомплектующих из SMC.
Бренд Tehnotron отвечает за соответствие высоким международным стандартам качества, что регулярно подтверждается обновляемым перечнем сертификатов и независимым органом оценки United Registrar of Systems Ltd. (URS Certification), благодаря контролю сырья, материалов и входящих комплектующих. Производственный потенциал в концерне позволяют конструировать и собирать все элементы самостоятельно в Набережных Челнах, не привлекая сторонние организации.
В настоящее время Технотрон в основном ориентированы на активное сотрудничество с такими автомобильными марками как ПАО «КАМАЗ», ОАО «МАЗ», «Группа ГАЗ», DAIMLER KAMAZ RUS и АЗ «УРАЛ». Компания стремится выйти на стабильный рост объемов производства, освоить также и региональные рынки и консолидировать автопромышленность.
Ассортимент:
- Система охлаждения
- Система питания
- Оперение кабины (экстерьер а/м 5490)
- Принадлежности кабины
- Элементы подвески
- Тягово-сцепные устройства
- Электрика
- Седельно-сцепные устройства
- Троллейный шинопровод и многое другое
На складах : 6690 шт.
На складах : 1150 шт.
На складах : 16 шт.
На складах : 17 шт.
На складах : 1790 шт.
На складах : 416 шт.
На складах : 18 шт.
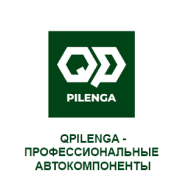
PILENGA — это бренд, который с 1947 года занимает лидирующие позиции в автомобильной промышленности. Компания была основана в Италии и изначально специализировалась на производстве металлических деталей для автомобилей.
С самого начала своей деятельности PILENGA делала упор на качество, надёжность и безопасность своей продукции. Компания разрабатывала детали, которые могли выдерживать высокие нагрузки.
Со временем ассортимент продукции PILENGA расширился, и сегодня она является одним из ведущих производителей тормозных дисков, барабанов и фильтров для легковых и грузовых автомобилей. Продукция компании поставляется на крупные автомобильные заводы в Европе и США.
PILENGA уделяет особое внимание созданию компонентов для грузовых автомобилей, понимая, насколько важно их качество и надёжность при эксплуатации в экстремальных условиях. Благодаря глубоким знаниям в области металлургии и строгому соблюдению стандартов качества, компания производит продукцию, которая соответствует самым высоким требованиям.
Применение автоматизированных систем контроля, роботизированных производственных процессов и многоэтапного тестирования позволяет существенно сократить количество бракованных изделий и гарантировать стабильное качество каждой детали.
Фильтры PILENGA подходят как для российских, так и для иностранных коммерческих автомобилей. Они совместимы с популярными европейскими моделями, такими как Ford Transit, MAN, Iveco, Mercedes-Benz, DAF и другими, а также с отечественными грузовиками ГАЗ, КАМАЗ и современными коммерческими автомобилями Sollers — Атлант и АРГО.
Такое разнообразие моделей позволяет компании удовлетворять потребности различных сегментов рынка и обеспечивать эффективную фильтрацию в любых условиях эксплуатации.
Производственные мощности компании находятся в Европе и Китае. На предприятиях регулярно обновляется оборудование и внедряются передовые технологии. С 2017 года активно применяется система 3D-проектирования деталей подвески, что значительно ускоряет разработку и вывод новых продуктов на рынок. Это позволяет компании быть гибкой и оперативно реагировать на запросы клиентов. Компания сотрудничает с известными автопроизводителями, такими как Chrysler и Harley Davidson. Она также успешно развивается на российском рынке и в странах СНГ, предлагая доступные цены и проверенное качество.
Успех компании PILENGA основан на работе научно-исследовательского центра, который занимается разработкой новых сплавов, улучшением технологий обработки металлов и внедрением цифровых решений в производственный процесс.
В ближайшие десять лет компания планирует достичь значительных результатов: расширить линейку товаров, сделать производство более экологичным и укрепить свои позиции на международной арене.
Особое внимание будет уделено использованию цифровых технологий и внедрению инноваций, что позволит компании оставаться конкурентоспособной в условиях быстрого развития автомобильной промышленности.
Сегодня PILENGA — это не просто поставщик деталей, а высокотехнологичная компания с богатым опытом и безупречной репутацией. Выбирая продукцию этой марки, клиенты могут быть уверены в надёжности и безопасности своих автомобилей. При этом бренд остаётся верен своим принципам, постоянно совершенствуясь и развиваясь.
Ассортимент:
- Амортизатор
- Барабан тормозной
- Диск тормозной
- Колодки тормозные
- Крестовина
- Механизм рулевой
- Муфта сцепления
- Наконечник рулевой тяги
- Насос водяной
- Насос отопителя салона
- Натяжитель ремня
- Опора шаровая
- Подшипник
- Привод передних колес
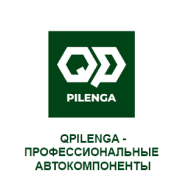
PILENGA — это бренд, который с 1947 года занимает лидирующие позиции в автомобильной промышленности. Компания была основана в Италии и изначально специализировалась на производстве металлических деталей для автомобилей.
С самого начала своей деятельности PILENGA делала упор на качество, надёжность и безопасность своей продукции. Компания разрабатывала детали, которые могли выдерживать высокие нагрузки.
Со временем ассортимент продукции PILENGA расширился, и сегодня она является одним из ведущих производителей тормозных дисков, барабанов и фильтров для легковых и грузовых автомобилей. Продукция компании поставляется на крупные автомобильные заводы в Европе и США.
PILENGA уделяет особое внимание созданию компонентов для грузовых автомобилей, понимая, насколько важно их качество и надёжность при эксплуатации в экстремальных условиях. Благодаря глубоким знаниям в области металлургии и строгому соблюдению стандартов качества, компания производит продукцию, которая соответствует самым высоким требованиям.
Применение автоматизированных систем контроля, роботизированных производственных процессов и многоэтапного тестирования позволяет существенно сократить количество бракованных изделий и гарантировать стабильное качество каждой детали.
Фильтры PILENGA подходят как для российских, так и для иностранных коммерческих автомобилей. Они совместимы с популярными европейскими моделями, такими как Ford Transit, MAN, Iveco, Mercedes-Benz, DAF и другими, а также с отечественными грузовиками ГАЗ, КАМАЗ и современными коммерческими автомобилями Sollers — Атлант и АРГО.
Такое разнообразие моделей позволяет компании удовлетворять потребности различных сегментов рынка и обеспечивать эффективную фильтрацию в любых условиях эксплуатации.
Производственные мощности компании находятся в Европе и Китае. На предприятиях регулярно обновляется оборудование и внедряются передовые технологии. С 2017 года активно применяется система 3D-проектирования деталей подвески, что значительно ускоряет разработку и вывод новых продуктов на рынок. Это позволяет компании быть гибкой и оперативно реагировать на запросы клиентов. Компания сотрудничает с известными автопроизводителями, такими как Chrysler и Harley Davidson. Она также успешно развивается на российском рынке и в странах СНГ, предлагая доступные цены и проверенное качество.
Успех компании PILENGA основан на работе научно-исследовательского центра, который занимается разработкой новых сплавов, улучшением технологий обработки металлов и внедрением цифровых решений в производственный процесс.
В ближайшие десять лет компания планирует достичь значительных результатов: расширить линейку товаров, сделать производство более экологичным и укрепить свои позиции на международной арене.
Особое внимание будет уделено использованию цифровых технологий и внедрению инноваций, что позволит компании оставаться конкурентоспособной в условиях быстрого развития автомобильной промышленности.
Сегодня PILENGA — это не просто поставщик деталей, а высокотехнологичная компания с богатым опытом и безупречной репутацией. Выбирая продукцию этой марки, клиенты могут быть уверены в надёжности и безопасности своих автомобилей. При этом бренд остаётся верен своим принципам, постоянно совершенствуясь и развиваясь.
Ассортимент:
- Амортизатор
- Барабан тормозной
- Диск тормозной
- Колодки тормозные
- Крестовина
- Механизм рулевой
- Муфта сцепления
- Наконечник рулевой тяги
- Насос водяной
- Насос отопителя салона
- Натяжитель ремня
- Опора шаровая
- Подшипник
- Привод передних колес
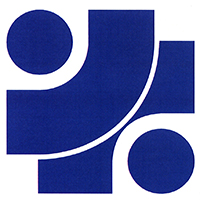
Производственное объединение «Трек» было основано в октябре 1995 года для выпуска комплектующих для легковых автомобилей. Основное направление деятельности ГРУППЫ «ТРЕК» — проектирование, производство и продажа элементов подвески, рулевого управления, трансмиссии, тормозной системы. Маркетинговые требования, переданные подразделениям НИОКР, трансформируются в новые инновационные изделия, проходящие все возможные виды проверок: компьютерное моделирование, стендовые и дорожные испытания. В новых конструкциях активно используются современные материалы, позволяющие нам предлагать нашим покупателям продукцию с улучшенными потребительскими свойствами по долговечности и надежности. Так, например, применение оригинальных решений при создании конструкции чехла ШРУС (наличие патента) и стойки стабилизатора, которые изготавливаются теперь из современных полимерных материалов, позволило создать изделие, по своим характеристикам значительно превышающее предыдущие аналоги. Не обделены вниманием и шарнирные соединения, конструкция которых постоянно совершенствуется. В результате покупатель получает инновационный продукт с улучшенными характеристиками. Процесс изготовления продукции включает в себя следующие виды производства: - прессовое – холодная и горячая объёмная штамповка, - механообрабатывающее – токарно-фрезерная группа оборудования, включая современные обрабатывающие центры EMAG, - переработки полимерных материалов – современное оборудование, в том числе термопласт–автоматы LG, - сборочное – с использованием высокопроизводительного специального оборудования, - инструментальное – с помощью современного обрабатывающего центра позволяет обеспечивать основное производство необходимым инструментом и оснасткой. Производственные мощности предприятия позволяют производить более миллиона шарнирных изделий в месяц. Контроль за качеством осуществляется на всех стадиях изготовления продукции (в том числе используется координатно-измерительная машина WENZEL). Система менеджмента качества предприятия сертифицирована на соответствие международному стандарту ISO 9001:2000 и национальному стандарту ГОСТ Р ИСО 9001:2001.
На складах : 177 шт.
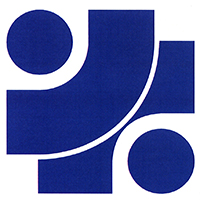
Производственное объединение «Трек» было основано в октябре 1995 года для выпуска комплектующих для легковых автомобилей. Основное направление деятельности ГРУППЫ «ТРЕК» — проектирование, производство и продажа элементов подвески, рулевого управления, трансмиссии, тормозной системы. Маркетинговые требования, переданные подразделениям НИОКР, трансформируются в новые инновационные изделия, проходящие все возможные виды проверок: компьютерное моделирование, стендовые и дорожные испытания. В новых конструкциях активно используются современные материалы, позволяющие нам предлагать нашим покупателям продукцию с улучшенными потребительскими свойствами по долговечности и надежности. Так, например, применение оригинальных решений при создании конструкции чехла ШРУС (наличие патента) и стойки стабилизатора, которые изготавливаются теперь из современных полимерных материалов, позволило создать изделие, по своим характеристикам значительно превышающее предыдущие аналоги. Не обделены вниманием и шарнирные соединения, конструкция которых постоянно совершенствуется. В результате покупатель получает инновационный продукт с улучшенными характеристиками. Процесс изготовления продукции включает в себя следующие виды производства: - прессовое – холодная и горячая объёмная штамповка, - механообрабатывающее – токарно-фрезерная группа оборудования, включая современные обрабатывающие центры EMAG, - переработки полимерных материалов – современное оборудование, в том числе термопласт–автоматы LG, - сборочное – с использованием высокопроизводительного специального оборудования, - инструментальное – с помощью современного обрабатывающего центра позволяет обеспечивать основное производство необходимым инструментом и оснасткой. Производственные мощности предприятия позволяют производить более миллиона шарнирных изделий в месяц. Контроль за качеством осуществляется на всех стадиях изготовления продукции (в том числе используется координатно-измерительная машина WENZEL). Система менеджмента качества предприятия сертифицирована на соответствие международному стандарту ISO 9001:2000 и национальному стандарту ГОСТ Р ИСО 9001:2001.
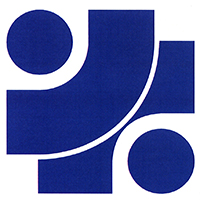
Производственное объединение «Трек» было основано в октябре 1995 года для выпуска комплектующих для легковых автомобилей. Основное направление деятельности ГРУППЫ «ТРЕК» — проектирование, производство и продажа элементов подвески, рулевого управления, трансмиссии, тормозной системы. Маркетинговые требования, переданные подразделениям НИОКР, трансформируются в новые инновационные изделия, проходящие все возможные виды проверок: компьютерное моделирование, стендовые и дорожные испытания. В новых конструкциях активно используются современные материалы, позволяющие нам предлагать нашим покупателям продукцию с улучшенными потребительскими свойствами по долговечности и надежности. Так, например, применение оригинальных решений при создании конструкции чехла ШРУС (наличие патента) и стойки стабилизатора, которые изготавливаются теперь из современных полимерных материалов, позволило создать изделие, по своим характеристикам значительно превышающее предыдущие аналоги. Не обделены вниманием и шарнирные соединения, конструкция которых постоянно совершенствуется. В результате покупатель получает инновационный продукт с улучшенными характеристиками. Процесс изготовления продукции включает в себя следующие виды производства: - прессовое – холодная и горячая объёмная штамповка, - механообрабатывающее – токарно-фрезерная группа оборудования, включая современные обрабатывающие центры EMAG, - переработки полимерных материалов – современное оборудование, в том числе термопласт–автоматы LG, - сборочное – с использованием высокопроизводительного специального оборудования, - инструментальное – с помощью современного обрабатывающего центра позволяет обеспечивать основное производство необходимым инструментом и оснасткой. Производственные мощности предприятия позволяют производить более миллиона шарнирных изделий в месяц. Контроль за качеством осуществляется на всех стадиях изготовления продукции (в том числе используется координатно-измерительная машина WENZEL). Система менеджмента качества предприятия сертифицирована на соответствие международному стандарту ISO 9001:2000 и национальному стандарту ГОСТ Р ИСО 9001:2001.
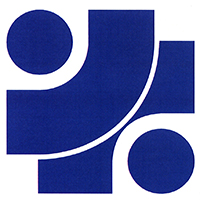
Производственное объединение «Трек» было основано в октябре 1995 года для выпуска комплектующих для легковых автомобилей. Основное направление деятельности ГРУППЫ «ТРЕК» — проектирование, производство и продажа элементов подвески, рулевого управления, трансмиссии, тормозной системы. Маркетинговые требования, переданные подразделениям НИОКР, трансформируются в новые инновационные изделия, проходящие все возможные виды проверок: компьютерное моделирование, стендовые и дорожные испытания. В новых конструкциях активно используются современные материалы, позволяющие нам предлагать нашим покупателям продукцию с улучшенными потребительскими свойствами по долговечности и надежности. Так, например, применение оригинальных решений при создании конструкции чехла ШРУС (наличие патента) и стойки стабилизатора, которые изготавливаются теперь из современных полимерных материалов, позволило создать изделие, по своим характеристикам значительно превышающее предыдущие аналоги. Не обделены вниманием и шарнирные соединения, конструкция которых постоянно совершенствуется. В результате покупатель получает инновационный продукт с улучшенными характеристиками. Процесс изготовления продукции включает в себя следующие виды производства: - прессовое – холодная и горячая объёмная штамповка, - механообрабатывающее – токарно-фрезерная группа оборудования, включая современные обрабатывающие центры EMAG, - переработки полимерных материалов – современное оборудование, в том числе термопласт–автоматы LG, - сборочное – с использованием высокопроизводительного специального оборудования, - инструментальное – с помощью современного обрабатывающего центра позволяет обеспечивать основное производство необходимым инструментом и оснасткой. Производственные мощности предприятия позволяют производить более миллиона шарнирных изделий в месяц. Контроль за качеством осуществляется на всех стадиях изготовления продукции (в том числе используется координатно-измерительная машина WENZEL). Система менеджмента качества предприятия сертифицирована на соответствие международному стандарту ISO 9001:2000 и национальному стандарту ГОСТ Р ИСО 9001:2001.
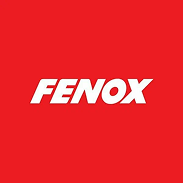
Компания FENOX начала свой путь в 1989 году, когда на постсоветском пространстве появилась небольшая фирма, выпускавшая гидравлические цилиндры для автомобилей ВАЗ. С тех пор компания прошла долгий путь развития — от узкоспециализированного производителя до международного концерна с современными заводами в Беларуси, России и Германии. В 1996 году FENOX сделала важный шаг, приобретя оборудование немецкой Bremse Hydraulic, что позволило значительно повысить качество продукции и выйти на рынки Европы и Америки. Сегодня FENOX — это более 12 современных производственных площадок и тысячи сотрудников, среди которых сотни инженеров, работающих над инновационными решениями и расширением ассортимента.
Ассортимент продукции FENOX насчитывает более 5000 наименований автокомпонентов, охватывающих все ключевые системы автомобиля. Компания производит детали для тормозных систем, электрических и охлаждающих систем, подвески, трансмиссии и рулевого управления. В числе выпускаемых изделий — амортизаторы, тормозные диски и колодки, гидроцилиндры, генераторы, стартеры, свечи зажигания, рулевые рейки, насосы, муфты сцепления, вентиляторы отопления и охлаждения, а также комплектующие для карданных шарниров и многое другое. Продукция ориентирована на широкий спектр техники: от легковых автомобилей ВАЗ и зарубежных брендов до грузовиков КАМАЗ, МАЗ, ГАЗ и УАЗ.
FENOX известна своей приверженностью качеству и инновациям. Компания обладает собственным конструкторским бюро и испытательным центром, аккредитованным по международным стандартам, что гарантирует надежность и безопасность выпускаемых изделий. Сертификация по ISO 9001 и соответствие требованиям VDA 6.1 позволяют поставлять продукцию не только на вторичный рынок, но и на конвейеры ведущих мировых автопроизводителей, таких как Volkswagen, Renault, General Motors и другие.
Сегодня FENOX экспортирует свою продукцию более чем в 50 стран мира, укрепляя позиции на международном рынке и продолжая расширять ассортимент. В планах компании — дальнейшее внедрение современных технологий, развитие производства и создание новых решений, которые помогут сделать автомобили еще более надежными и безопасными. История FENOX — это пример успешного развития, основанного на качестве, инновациях и стремлении удовлетворять потребности самых требовательных клиентов.
Ассортимент:
- Система охлаждения
- Электрическая система
- Система рулевого управления
- Система подвески
- Система трансмиссии
- Главные тормозные цилиндры
- Датчики ABS
- Лямбда-зонды
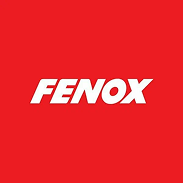
Компания FENOX начала свой путь в 1989 году, когда на постсоветском пространстве появилась небольшая фирма, выпускавшая гидравлические цилиндры для автомобилей ВАЗ. С тех пор компания прошла долгий путь развития — от узкоспециализированного производителя до международного концерна с современными заводами в Беларуси, России и Германии. В 1996 году FENOX сделала важный шаг, приобретя оборудование немецкой Bremse Hydraulic, что позволило значительно повысить качество продукции и выйти на рынки Европы и Америки. Сегодня FENOX — это более 12 современных производственных площадок и тысячи сотрудников, среди которых сотни инженеров, работающих над инновационными решениями и расширением ассортимента.
Ассортимент продукции FENOX насчитывает более 5000 наименований автокомпонентов, охватывающих все ключевые системы автомобиля. Компания производит детали для тормозных систем, электрических и охлаждающих систем, подвески, трансмиссии и рулевого управления. В числе выпускаемых изделий — амортизаторы, тормозные диски и колодки, гидроцилиндры, генераторы, стартеры, свечи зажигания, рулевые рейки, насосы, муфты сцепления, вентиляторы отопления и охлаждения, а также комплектующие для карданных шарниров и многое другое. Продукция ориентирована на широкий спектр техники: от легковых автомобилей ВАЗ и зарубежных брендов до грузовиков КАМАЗ, МАЗ, ГАЗ и УАЗ.
FENOX известна своей приверженностью качеству и инновациям. Компания обладает собственным конструкторским бюро и испытательным центром, аккредитованным по международным стандартам, что гарантирует надежность и безопасность выпускаемых изделий. Сертификация по ISO 9001 и соответствие требованиям VDA 6.1 позволяют поставлять продукцию не только на вторичный рынок, но и на конвейеры ведущих мировых автопроизводителей, таких как Volkswagen, Renault, General Motors и другие.
Сегодня FENOX экспортирует свою продукцию более чем в 50 стран мира, укрепляя позиции на международном рынке и продолжая расширять ассортимент. В планах компании — дальнейшее внедрение современных технологий, развитие производства и создание новых решений, которые помогут сделать автомобили еще более надежными и безопасными. История FENOX — это пример успешного развития, основанного на качестве, инновациях и стремлении удовлетворять потребности самых требовательных клиентов.
Ассортимент:
- Система охлаждения
- Электрическая система
- Система рулевого управления
- Система подвески
- Система трансмиссии
- Главные тормозные цилиндры
- Датчики ABS
- Лямбда-зонды
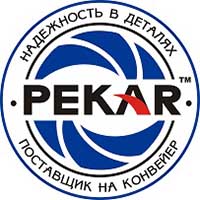
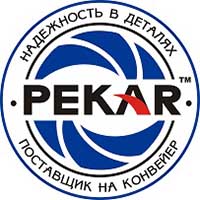
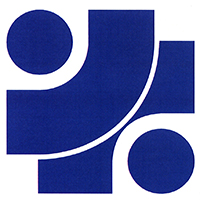
Производственное объединение «Трек» было основано в октябре 1995 года для выпуска комплектующих для легковых автомобилей. Основное направление деятельности ГРУППЫ «ТРЕК» — проектирование, производство и продажа элементов подвески, рулевого управления, трансмиссии, тормозной системы. Маркетинговые требования, переданные подразделениям НИОКР, трансформируются в новые инновационные изделия, проходящие все возможные виды проверок: компьютерное моделирование, стендовые и дорожные испытания. В новых конструкциях активно используются современные материалы, позволяющие нам предлагать нашим покупателям продукцию с улучшенными потребительскими свойствами по долговечности и надежности. Так, например, применение оригинальных решений при создании конструкции чехла ШРУС (наличие патента) и стойки стабилизатора, которые изготавливаются теперь из современных полимерных материалов, позволило создать изделие, по своим характеристикам значительно превышающее предыдущие аналоги. Не обделены вниманием и шарнирные соединения, конструкция которых постоянно совершенствуется. В результате покупатель получает инновационный продукт с улучшенными характеристиками. Процесс изготовления продукции включает в себя следующие виды производства: - прессовое – холодная и горячая объёмная штамповка, - механообрабатывающее – токарно-фрезерная группа оборудования, включая современные обрабатывающие центры EMAG, - переработки полимерных материалов – современное оборудование, в том числе термопласт–автоматы LG, - сборочное – с использованием высокопроизводительного специального оборудования, - инструментальное – с помощью современного обрабатывающего центра позволяет обеспечивать основное производство необходимым инструментом и оснасткой. Производственные мощности предприятия позволяют производить более миллиона шарнирных изделий в месяц. Контроль за качеством осуществляется на всех стадиях изготовления продукции (в том числе используется координатно-измерительная машина WENZEL). Система менеджмента качества предприятия сертифицирована на соответствие международному стандарту ISO 9001:2000 и национальному стандарту ГОСТ Р ИСО 9001:2001.
На складах : 23 шт.
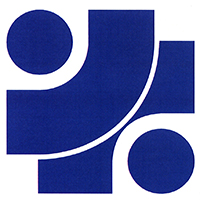
Производственное объединение «Трек» было основано в октябре 1995 года для выпуска комплектующих для легковых автомобилей. Основное направление деятельности ГРУППЫ «ТРЕК» — проектирование, производство и продажа элементов подвески, рулевого управления, трансмиссии, тормозной системы. Маркетинговые требования, переданные подразделениям НИОКР, трансформируются в новые инновационные изделия, проходящие все возможные виды проверок: компьютерное моделирование, стендовые и дорожные испытания. В новых конструкциях активно используются современные материалы, позволяющие нам предлагать нашим покупателям продукцию с улучшенными потребительскими свойствами по долговечности и надежности. Так, например, применение оригинальных решений при создании конструкции чехла ШРУС (наличие патента) и стойки стабилизатора, которые изготавливаются теперь из современных полимерных материалов, позволило создать изделие, по своим характеристикам значительно превышающее предыдущие аналоги. Не обделены вниманием и шарнирные соединения, конструкция которых постоянно совершенствуется. В результате покупатель получает инновационный продукт с улучшенными характеристиками. Процесс изготовления продукции включает в себя следующие виды производства: - прессовое – холодная и горячая объёмная штамповка, - механообрабатывающее – токарно-фрезерная группа оборудования, включая современные обрабатывающие центры EMAG, - переработки полимерных материалов – современное оборудование, в том числе термопласт–автоматы LG, - сборочное – с использованием высокопроизводительного специального оборудования, - инструментальное – с помощью современного обрабатывающего центра позволяет обеспечивать основное производство необходимым инструментом и оснасткой. Производственные мощности предприятия позволяют производить более миллиона шарнирных изделий в месяц. Контроль за качеством осуществляется на всех стадиях изготовления продукции (в том числе используется координатно-измерительная машина WENZEL). Система менеджмента качества предприятия сертифицирована на соответствие международному стандарту ISO 9001:2000 и национальному стандарту ГОСТ Р ИСО 9001:2001.
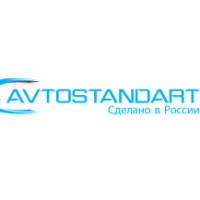
AVTOSTANDART завоевал доверие автовладельцев как производитель доступных и надежных автозапчастей, сочетающий международные стандарты качества с адаптацией к местным условиям эксплуатации. История бренда насчитывает более 20 лет, начиная с организации собственных производственных линий в Тольятти в 2005 году, где и сегодня выпускается значительная часть продукции для автомобилей ВАЗ. Специализация AVTOSTANDART изначально фокусировалась на деталях для российских автомобилей, таких как пружины подвески, тормозные колодки, рулевые наконечники и фильтры, но сегодня ассортимент включает компоненты для иномарок, включая коммерческий транспорт Mercedes, Volkswagen и Ford.
Философия бренда строится на принципе «неубиваемости» в условиях реальных дорог. Продукция проектируется с учетом специфики эксплуатации в регионах с плохим покрытием, перепадами температур и высокой влажностью. Например, тормозные колодки AVTOSTANDART производятся по безасбестовой технологии, обеспечивающей эффективное и бесшумное торможение даже при перегрузках, а их состав оптимизирован для минимизации износа дисков. Такие решения проходят многоступенчатые испытания на полигонах и в лабораториях, включая тесты на холодоустойчивость, абразивный износ и термостойкость, что гарантирует соответствие стандартам ECE R-90 и ДСТУ.
Система контроля качества — ключевой актив бренда. Все заводы, включая зарубежные партнерские площадки, работают по единым стандартам ISO 9001, IATF и ISO/TS 16949, что подтверждено сертификатами. Технологический процесс включает входной контроль материалов, прессовку с точным соблюдением температурных режимов, рентгенографию металлоконструкций и финальные ресурсные тесты. Это исключает брак, но рынок столкнулся с проблемой подделок. Для защиты потребителя AVTOSTANDART внедрил многоуровневую систему идентификации: голографические наклейки, QR-коды для верификации на официальном сайте, микротиснение на упаковке и лазерную гравировку на деталях.
Продукция бренда рассчитана на разные сценарии использования. Для повседневной эксплуатации в городском цикле или на трассе подходят стандартные линии, демонстрирующие ресурс, превышающий гарантийный срок при своевременном ТО. Однако для экстремальных режимов — таких, как спортивная езда, постоянные перегрузки или работа в условиях бездорожья — инженеры рекомендуют премиальные серии с усиленными характеристиками. Отзывы клиентов подчеркивают оптимальное соотношение цены и качества, хотя некоторые негативные оценки связаны с установкой неоригинальных деталей или нарушением регламентов обслуживания.
АвтоАльянс — ваш надежный партнер в мире автозапчастей. Мы предлагаем обширный каталог продукции бренда — от тормозных систем до компонентов подвески — с гарантией подлинности и профессиональными консультациями по установке. Наши клиенты получают доступ к деталям, протестированным в реальных дорожных условиях, по конкурентным ценам и с гибкой системой скидок для оптовых заказов.
Ассортимент:
- Гидравлика
- Глушители
- ДВС
- Карданные валы
- Комплекты поршневых колец
- КПП
- Опоры
- Подвеска
- Радиаторы
- Рулевая система
- Стойки и амортизаторы
- Ступицы и подшипники колес
- Тормозная система
- Трансмиссия
- Усиленный ступичный узел
- Фильтры и прочее
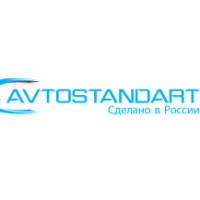
AVTOSTANDART завоевал доверие автовладельцев как производитель доступных и надежных автозапчастей, сочетающий международные стандарты качества с адаптацией к местным условиям эксплуатации. История бренда насчитывает более 20 лет, начиная с организации собственных производственных линий в Тольятти в 2005 году, где и сегодня выпускается значительная часть продукции для автомобилей ВАЗ. Специализация AVTOSTANDART изначально фокусировалась на деталях для российских автомобилей, таких как пружины подвески, тормозные колодки, рулевые наконечники и фильтры, но сегодня ассортимент включает компоненты для иномарок, включая коммерческий транспорт Mercedes, Volkswagen и Ford.
Философия бренда строится на принципе «неубиваемости» в условиях реальных дорог. Продукция проектируется с учетом специфики эксплуатации в регионах с плохим покрытием, перепадами температур и высокой влажностью. Например, тормозные колодки AVTOSTANDART производятся по безасбестовой технологии, обеспечивающей эффективное и бесшумное торможение даже при перегрузках, а их состав оптимизирован для минимизации износа дисков. Такие решения проходят многоступенчатые испытания на полигонах и в лабораториях, включая тесты на холодоустойчивость, абразивный износ и термостойкость, что гарантирует соответствие стандартам ECE R-90 и ДСТУ.
Система контроля качества — ключевой актив бренда. Все заводы, включая зарубежные партнерские площадки, работают по единым стандартам ISO 9001, IATF и ISO/TS 16949, что подтверждено сертификатами. Технологический процесс включает входной контроль материалов, прессовку с точным соблюдением температурных режимов, рентгенографию металлоконструкций и финальные ресурсные тесты. Это исключает брак, но рынок столкнулся с проблемой подделок. Для защиты потребителя AVTOSTANDART внедрил многоуровневую систему идентификации: голографические наклейки, QR-коды для верификации на официальном сайте, микротиснение на упаковке и лазерную гравировку на деталях.
Продукция бренда рассчитана на разные сценарии использования. Для повседневной эксплуатации в городском цикле или на трассе подходят стандартные линии, демонстрирующие ресурс, превышающий гарантийный срок при своевременном ТО. Однако для экстремальных режимов — таких, как спортивная езда, постоянные перегрузки или работа в условиях бездорожья — инженеры рекомендуют премиальные серии с усиленными характеристиками. Отзывы клиентов подчеркивают оптимальное соотношение цены и качества, хотя некоторые негативные оценки связаны с установкой неоригинальных деталей или нарушением регламентов обслуживания.
АвтоАльянс — ваш надежный партнер в мире автозапчастей. Мы предлагаем обширный каталог продукции бренда — от тормозных систем до компонентов подвески — с гарантией подлинности и профессиональными консультациями по установке. Наши клиенты получают доступ к деталям, протестированным в реальных дорожных условиях, по конкурентным ценам и с гибкой системой скидок для оптовых заказов.
Ассортимент:
- Гидравлика
- Глушители
- ДВС
- Карданные валы
- Комплекты поршневых колец
- КПП
- Опоры
- Подвеска
- Радиаторы
- Рулевая система
- Стойки и амортизаторы
- Ступицы и подшипники колес
- Тормозная система
- Трансмиссия
- Усиленный ступичный узел
- Фильтры и прочее
На складах : 18 шт.
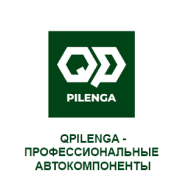
PILENGA — это бренд, который с 1947 года занимает лидирующие позиции в автомобильной промышленности. Компания была основана в Италии и изначально специализировалась на производстве металлических деталей для автомобилей.
С самого начала своей деятельности PILENGA делала упор на качество, надёжность и безопасность своей продукции. Компания разрабатывала детали, которые могли выдерживать высокие нагрузки.
Со временем ассортимент продукции PILENGA расширился, и сегодня она является одним из ведущих производителей тормозных дисков, барабанов и фильтров для легковых и грузовых автомобилей. Продукция компании поставляется на крупные автомобильные заводы в Европе и США.
PILENGA уделяет особое внимание созданию компонентов для грузовых автомобилей, понимая, насколько важно их качество и надёжность при эксплуатации в экстремальных условиях. Благодаря глубоким знаниям в области металлургии и строгому соблюдению стандартов качества, компания производит продукцию, которая соответствует самым высоким требованиям.
Применение автоматизированных систем контроля, роботизированных производственных процессов и многоэтапного тестирования позволяет существенно сократить количество бракованных изделий и гарантировать стабильное качество каждой детали.
Фильтры PILENGA подходят как для российских, так и для иностранных коммерческих автомобилей. Они совместимы с популярными европейскими моделями, такими как Ford Transit, MAN, Iveco, Mercedes-Benz, DAF и другими, а также с отечественными грузовиками ГАЗ, КАМАЗ и современными коммерческими автомобилями Sollers — Атлант и АРГО.
Такое разнообразие моделей позволяет компании удовлетворять потребности различных сегментов рынка и обеспечивать эффективную фильтрацию в любых условиях эксплуатации.
Производственные мощности компании находятся в Европе и Китае. На предприятиях регулярно обновляется оборудование и внедряются передовые технологии. С 2017 года активно применяется система 3D-проектирования деталей подвески, что значительно ускоряет разработку и вывод новых продуктов на рынок. Это позволяет компании быть гибкой и оперативно реагировать на запросы клиентов. Компания сотрудничает с известными автопроизводителями, такими как Chrysler и Harley Davidson. Она также успешно развивается на российском рынке и в странах СНГ, предлагая доступные цены и проверенное качество.
Успех компании PILENGA основан на работе научно-исследовательского центра, который занимается разработкой новых сплавов, улучшением технологий обработки металлов и внедрением цифровых решений в производственный процесс.
В ближайшие десять лет компания планирует достичь значительных результатов: расширить линейку товаров, сделать производство более экологичным и укрепить свои позиции на международной арене.
Особое внимание будет уделено использованию цифровых технологий и внедрению инноваций, что позволит компании оставаться конкурентоспособной в условиях быстрого развития автомобильной промышленности.
Сегодня PILENGA — это не просто поставщик деталей, а высокотехнологичная компания с богатым опытом и безупречной репутацией. Выбирая продукцию этой марки, клиенты могут быть уверены в надёжности и безопасности своих автомобилей. При этом бренд остаётся верен своим принципам, постоянно совершенствуясь и развиваясь.
Ассортимент:
- Амортизатор
- Барабан тормозной
- Диск тормозной
- Колодки тормозные
- Крестовина
- Механизм рулевой
- Муфта сцепления
- Наконечник рулевой тяги
- Насос водяной
- Насос отопителя салона
- Натяжитель ремня
- Опора шаровая
- Подшипник
- Привод передних колес
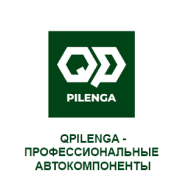
PILENGA — это бренд, который с 1947 года занимает лидирующие позиции в автомобильной промышленности. Компания была основана в Италии и изначально специализировалась на производстве металлических деталей для автомобилей.
С самого начала своей деятельности PILENGA делала упор на качество, надёжность и безопасность своей продукции. Компания разрабатывала детали, которые могли выдерживать высокие нагрузки.
Со временем ассортимент продукции PILENGA расширился, и сегодня она является одним из ведущих производителей тормозных дисков, барабанов и фильтров для легковых и грузовых автомобилей. Продукция компании поставляется на крупные автомобильные заводы в Европе и США.
PILENGA уделяет особое внимание созданию компонентов для грузовых автомобилей, понимая, насколько важно их качество и надёжность при эксплуатации в экстремальных условиях. Благодаря глубоким знаниям в области металлургии и строгому соблюдению стандартов качества, компания производит продукцию, которая соответствует самым высоким требованиям.
Применение автоматизированных систем контроля, роботизированных производственных процессов и многоэтапного тестирования позволяет существенно сократить количество бракованных изделий и гарантировать стабильное качество каждой детали.
Фильтры PILENGA подходят как для российских, так и для иностранных коммерческих автомобилей. Они совместимы с популярными европейскими моделями, такими как Ford Transit, MAN, Iveco, Mercedes-Benz, DAF и другими, а также с отечественными грузовиками ГАЗ, КАМАЗ и современными коммерческими автомобилями Sollers — Атлант и АРГО.
Такое разнообразие моделей позволяет компании удовлетворять потребности различных сегментов рынка и обеспечивать эффективную фильтрацию в любых условиях эксплуатации.
Производственные мощности компании находятся в Европе и Китае. На предприятиях регулярно обновляется оборудование и внедряются передовые технологии. С 2017 года активно применяется система 3D-проектирования деталей подвески, что значительно ускоряет разработку и вывод новых продуктов на рынок. Это позволяет компании быть гибкой и оперативно реагировать на запросы клиентов. Компания сотрудничает с известными автопроизводителями, такими как Chrysler и Harley Davidson. Она также успешно развивается на российском рынке и в странах СНГ, предлагая доступные цены и проверенное качество.
Успех компании PILENGA основан на работе научно-исследовательского центра, который занимается разработкой новых сплавов, улучшением технологий обработки металлов и внедрением цифровых решений в производственный процесс.
В ближайшие десять лет компания планирует достичь значительных результатов: расширить линейку товаров, сделать производство более экологичным и укрепить свои позиции на международной арене.
Особое внимание будет уделено использованию цифровых технологий и внедрению инноваций, что позволит компании оставаться конкурентоспособной в условиях быстрого развития автомобильной промышленности.
Сегодня PILENGA — это не просто поставщик деталей, а высокотехнологичная компания с богатым опытом и безупречной репутацией. Выбирая продукцию этой марки, клиенты могут быть уверены в надёжности и безопасности своих автомобилей. При этом бренд остаётся верен своим принципам, постоянно совершенствуясь и развиваясь.
Ассортимент:
- Амортизатор
- Барабан тормозной
- Диск тормозной
- Колодки тормозные
- Крестовина
- Механизм рулевой
- Муфта сцепления
- Наконечник рулевой тяги
- Насос водяной
- Насос отопителя салона
- Натяжитель ремня
- Опора шаровая
- Подшипник
- Привод передних колес
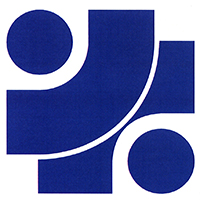
Производственное объединение «Трек» было основано в октябре 1995 года для выпуска комплектующих для легковых автомобилей. Основное направление деятельности ГРУППЫ «ТРЕК» — проектирование, производство и продажа элементов подвески, рулевого управления, трансмиссии, тормозной системы. Маркетинговые требования, переданные подразделениям НИОКР, трансформируются в новые инновационные изделия, проходящие все возможные виды проверок: компьютерное моделирование, стендовые и дорожные испытания. В новых конструкциях активно используются современные материалы, позволяющие нам предлагать нашим покупателям продукцию с улучшенными потребительскими свойствами по долговечности и надежности. Так, например, применение оригинальных решений при создании конструкции чехла ШРУС (наличие патента) и стойки стабилизатора, которые изготавливаются теперь из современных полимерных материалов, позволило создать изделие, по своим характеристикам значительно превышающее предыдущие аналоги. Не обделены вниманием и шарнирные соединения, конструкция которых постоянно совершенствуется. В результате покупатель получает инновационный продукт с улучшенными характеристиками. Процесс изготовления продукции включает в себя следующие виды производства: - прессовое – холодная и горячая объёмная штамповка, - механообрабатывающее – токарно-фрезерная группа оборудования, включая современные обрабатывающие центры EMAG, - переработки полимерных материалов – современное оборудование, в том числе термопласт–автоматы LG, - сборочное – с использованием высокопроизводительного специального оборудования, - инструментальное – с помощью современного обрабатывающего центра позволяет обеспечивать основное производство необходимым инструментом и оснасткой. Производственные мощности предприятия позволяют производить более миллиона шарнирных изделий в месяц. Контроль за качеством осуществляется на всех стадиях изготовления продукции (в том числе используется координатно-измерительная машина WENZEL). Система менеджмента качества предприятия сертифицирована на соответствие международному стандарту ISO 9001:2000 и национальному стандарту ГОСТ Р ИСО 9001:2001.
На складах : 177 шт.
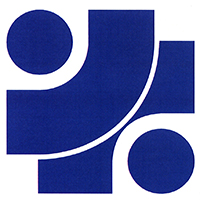
Производственное объединение «Трек» было основано в октябре 1995 года для выпуска комплектующих для легковых автомобилей. Основное направление деятельности ГРУППЫ «ТРЕК» — проектирование, производство и продажа элементов подвески, рулевого управления, трансмиссии, тормозной системы. Маркетинговые требования, переданные подразделениям НИОКР, трансформируются в новые инновационные изделия, проходящие все возможные виды проверок: компьютерное моделирование, стендовые и дорожные испытания. В новых конструкциях активно используются современные материалы, позволяющие нам предлагать нашим покупателям продукцию с улучшенными потребительскими свойствами по долговечности и надежности. Так, например, применение оригинальных решений при создании конструкции чехла ШРУС (наличие патента) и стойки стабилизатора, которые изготавливаются теперь из современных полимерных материалов, позволило создать изделие, по своим характеристикам значительно превышающее предыдущие аналоги. Не обделены вниманием и шарнирные соединения, конструкция которых постоянно совершенствуется. В результате покупатель получает инновационный продукт с улучшенными характеристиками. Процесс изготовления продукции включает в себя следующие виды производства: - прессовое – холодная и горячая объёмная штамповка, - механообрабатывающее – токарно-фрезерная группа оборудования, включая современные обрабатывающие центры EMAG, - переработки полимерных материалов – современное оборудование, в том числе термопласт–автоматы LG, - сборочное – с использованием высокопроизводительного специального оборудования, - инструментальное – с помощью современного обрабатывающего центра позволяет обеспечивать основное производство необходимым инструментом и оснасткой. Производственные мощности предприятия позволяют производить более миллиона шарнирных изделий в месяц. Контроль за качеством осуществляется на всех стадиях изготовления продукции (в том числе используется координатно-измерительная машина WENZEL). Система менеджмента качества предприятия сертифицирована на соответствие международному стандарту ISO 9001:2000 и национальному стандарту ГОСТ Р ИСО 9001:2001.
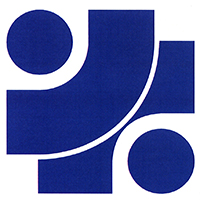
Производственное объединение «Трек» было основано в октябре 1995 года для выпуска комплектующих для легковых автомобилей. Основное направление деятельности ГРУППЫ «ТРЕК» — проектирование, производство и продажа элементов подвески, рулевого управления, трансмиссии, тормозной системы. Маркетинговые требования, переданные подразделениям НИОКР, трансформируются в новые инновационные изделия, проходящие все возможные виды проверок: компьютерное моделирование, стендовые и дорожные испытания. В новых конструкциях активно используются современные материалы, позволяющие нам предлагать нашим покупателям продукцию с улучшенными потребительскими свойствами по долговечности и надежности. Так, например, применение оригинальных решений при создании конструкции чехла ШРУС (наличие патента) и стойки стабилизатора, которые изготавливаются теперь из современных полимерных материалов, позволило создать изделие, по своим характеристикам значительно превышающее предыдущие аналоги. Не обделены вниманием и шарнирные соединения, конструкция которых постоянно совершенствуется. В результате покупатель получает инновационный продукт с улучшенными характеристиками. Процесс изготовления продукции включает в себя следующие виды производства: - прессовое – холодная и горячая объёмная штамповка, - механообрабатывающее – токарно-фрезерная группа оборудования, включая современные обрабатывающие центры EMAG, - переработки полимерных материалов – современное оборудование, в том числе термопласт–автоматы LG, - сборочное – с использованием высокопроизводительного специального оборудования, - инструментальное – с помощью современного обрабатывающего центра позволяет обеспечивать основное производство необходимым инструментом и оснасткой. Производственные мощности предприятия позволяют производить более миллиона шарнирных изделий в месяц. Контроль за качеством осуществляется на всех стадиях изготовления продукции (в том числе используется координатно-измерительная машина WENZEL). Система менеджмента качества предприятия сертифицирована на соответствие международному стандарту ISO 9001:2000 и национальному стандарту ГОСТ Р ИСО 9001:2001.
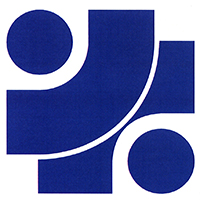
Производственное объединение «Трек» было основано в октябре 1995 года для выпуска комплектующих для легковых автомобилей. Основное направление деятельности ГРУППЫ «ТРЕК» — проектирование, производство и продажа элементов подвески, рулевого управления, трансмиссии, тормозной системы. Маркетинговые требования, переданные подразделениям НИОКР, трансформируются в новые инновационные изделия, проходящие все возможные виды проверок: компьютерное моделирование, стендовые и дорожные испытания. В новых конструкциях активно используются современные материалы, позволяющие нам предлагать нашим покупателям продукцию с улучшенными потребительскими свойствами по долговечности и надежности. Так, например, применение оригинальных решений при создании конструкции чехла ШРУС (наличие патента) и стойки стабилизатора, которые изготавливаются теперь из современных полимерных материалов, позволило создать изделие, по своим характеристикам значительно превышающее предыдущие аналоги. Не обделены вниманием и шарнирные соединения, конструкция которых постоянно совершенствуется. В результате покупатель получает инновационный продукт с улучшенными характеристиками. Процесс изготовления продукции включает в себя следующие виды производства: - прессовое – холодная и горячая объёмная штамповка, - механообрабатывающее – токарно-фрезерная группа оборудования, включая современные обрабатывающие центры EMAG, - переработки полимерных материалов – современное оборудование, в том числе термопласт–автоматы LG, - сборочное – с использованием высокопроизводительного специального оборудования, - инструментальное – с помощью современного обрабатывающего центра позволяет обеспечивать основное производство необходимым инструментом и оснасткой. Производственные мощности предприятия позволяют производить более миллиона шарнирных изделий в месяц. Контроль за качеством осуществляется на всех стадиях изготовления продукции (в том числе используется координатно-измерительная машина WENZEL). Система менеджмента качества предприятия сертифицирована на соответствие международному стандарту ISO 9001:2000 и национальному стандарту ГОСТ Р ИСО 9001:2001.
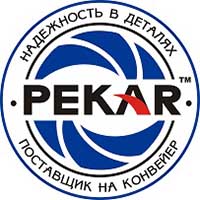
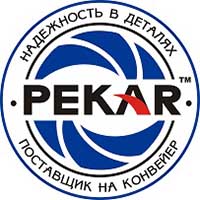
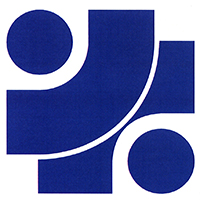
Производственное объединение «Трек» было основано в октябре 1995 года для выпуска комплектующих для легковых автомобилей. Основное направление деятельности ГРУППЫ «ТРЕК» — проектирование, производство и продажа элементов подвески, рулевого управления, трансмиссии, тормозной системы. Маркетинговые требования, переданные подразделениям НИОКР, трансформируются в новые инновационные изделия, проходящие все возможные виды проверок: компьютерное моделирование, стендовые и дорожные испытания. В новых конструкциях активно используются современные материалы, позволяющие нам предлагать нашим покупателям продукцию с улучшенными потребительскими свойствами по долговечности и надежности. Так, например, применение оригинальных решений при создании конструкции чехла ШРУС (наличие патента) и стойки стабилизатора, которые изготавливаются теперь из современных полимерных материалов, позволило создать изделие, по своим характеристикам значительно превышающее предыдущие аналоги. Не обделены вниманием и шарнирные соединения, конструкция которых постоянно совершенствуется. В результате покупатель получает инновационный продукт с улучшенными характеристиками. Процесс изготовления продукции включает в себя следующие виды производства: - прессовое – холодная и горячая объёмная штамповка, - механообрабатывающее – токарно-фрезерная группа оборудования, включая современные обрабатывающие центры EMAG, - переработки полимерных материалов – современное оборудование, в том числе термопласт–автоматы LG, - сборочное – с использованием высокопроизводительного специального оборудования, - инструментальное – с помощью современного обрабатывающего центра позволяет обеспечивать основное производство необходимым инструментом и оснасткой. Производственные мощности предприятия позволяют производить более миллиона шарнирных изделий в месяц. Контроль за качеством осуществляется на всех стадиях изготовления продукции (в том числе используется координатно-измерительная машина WENZEL). Система менеджмента качества предприятия сертифицирована на соответствие международному стандарту ISO 9001:2000 и национальному стандарту ГОСТ Р ИСО 9001:2001.
На складах : 23 шт.
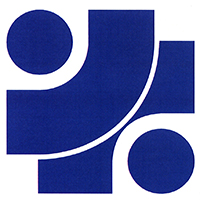
Производственное объединение «Трек» было основано в октябре 1995 года для выпуска комплектующих для легковых автомобилей. Основное направление деятельности ГРУППЫ «ТРЕК» — проектирование, производство и продажа элементов подвески, рулевого управления, трансмиссии, тормозной системы. Маркетинговые требования, переданные подразделениям НИОКР, трансформируются в новые инновационные изделия, проходящие все возможные виды проверок: компьютерное моделирование, стендовые и дорожные испытания. В новых конструкциях активно используются современные материалы, позволяющие нам предлагать нашим покупателям продукцию с улучшенными потребительскими свойствами по долговечности и надежности. Так, например, применение оригинальных решений при создании конструкции чехла ШРУС (наличие патента) и стойки стабилизатора, которые изготавливаются теперь из современных полимерных материалов, позволило создать изделие, по своим характеристикам значительно превышающее предыдущие аналоги. Не обделены вниманием и шарнирные соединения, конструкция которых постоянно совершенствуется. В результате покупатель получает инновационный продукт с улучшенными характеристиками. Процесс изготовления продукции включает в себя следующие виды производства: - прессовое – холодная и горячая объёмная штамповка, - механообрабатывающее – токарно-фрезерная группа оборудования, включая современные обрабатывающие центры EMAG, - переработки полимерных материалов – современное оборудование, в том числе термопласт–автоматы LG, - сборочное – с использованием высокопроизводительного специального оборудования, - инструментальное – с помощью современного обрабатывающего центра позволяет обеспечивать основное производство необходимым инструментом и оснасткой. Производственные мощности предприятия позволяют производить более миллиона шарнирных изделий в месяц. Контроль за качеством осуществляется на всех стадиях изготовления продукции (в том числе используется координатно-измерительная машина WENZEL). Система менеджмента качества предприятия сертифицирована на соответствие международному стандарту ISO 9001:2000 и национальному стандарту ГОСТ Р ИСО 9001:2001.
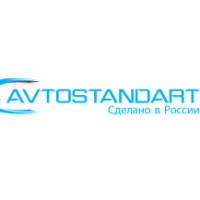
AVTOSTANDART завоевал доверие автовладельцев как производитель доступных и надежных автозапчастей, сочетающий международные стандарты качества с адаптацией к местным условиям эксплуатации. История бренда насчитывает более 20 лет, начиная с организации собственных производственных линий в Тольятти в 2005 году, где и сегодня выпускается значительная часть продукции для автомобилей ВАЗ. Специализация AVTOSTANDART изначально фокусировалась на деталях для российских автомобилей, таких как пружины подвески, тормозные колодки, рулевые наконечники и фильтры, но сегодня ассортимент включает компоненты для иномарок, включая коммерческий транспорт Mercedes, Volkswagen и Ford.
Философия бренда строится на принципе «неубиваемости» в условиях реальных дорог. Продукция проектируется с учетом специфики эксплуатации в регионах с плохим покрытием, перепадами температур и высокой влажностью. Например, тормозные колодки AVTOSTANDART производятся по безасбестовой технологии, обеспечивающей эффективное и бесшумное торможение даже при перегрузках, а их состав оптимизирован для минимизации износа дисков. Такие решения проходят многоступенчатые испытания на полигонах и в лабораториях, включая тесты на холодоустойчивость, абразивный износ и термостойкость, что гарантирует соответствие стандартам ECE R-90 и ДСТУ.
Система контроля качества — ключевой актив бренда. Все заводы, включая зарубежные партнерские площадки, работают по единым стандартам ISO 9001, IATF и ISO/TS 16949, что подтверждено сертификатами. Технологический процесс включает входной контроль материалов, прессовку с точным соблюдением температурных режимов, рентгенографию металлоконструкций и финальные ресурсные тесты. Это исключает брак, но рынок столкнулся с проблемой подделок. Для защиты потребителя AVTOSTANDART внедрил многоуровневую систему идентификации: голографические наклейки, QR-коды для верификации на официальном сайте, микротиснение на упаковке и лазерную гравировку на деталях.
Продукция бренда рассчитана на разные сценарии использования. Для повседневной эксплуатации в городском цикле или на трассе подходят стандартные линии, демонстрирующие ресурс, превышающий гарантийный срок при своевременном ТО. Однако для экстремальных режимов — таких, как спортивная езда, постоянные перегрузки или работа в условиях бездорожья — инженеры рекомендуют премиальные серии с усиленными характеристиками. Отзывы клиентов подчеркивают оптимальное соотношение цены и качества, хотя некоторые негативные оценки связаны с установкой неоригинальных деталей или нарушением регламентов обслуживания.
АвтоАльянс — ваш надежный партнер в мире автозапчастей. Мы предлагаем обширный каталог продукции бренда — от тормозных систем до компонентов подвески — с гарантией подлинности и профессиональными консультациями по установке. Наши клиенты получают доступ к деталям, протестированным в реальных дорожных условиях, по конкурентным ценам и с гибкой системой скидок для оптовых заказов.
Ассортимент:
- Гидравлика
- Глушители
- ДВС
- Карданные валы
- Комплекты поршневых колец
- КПП
- Опоры
- Подвеска
- Радиаторы
- Рулевая система
- Стойки и амортизаторы
- Ступицы и подшипники колес
- Тормозная система
- Трансмиссия
- Усиленный ступичный узел
- Фильтры и прочее
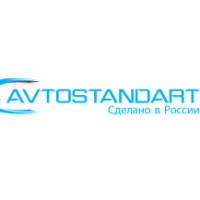
AVTOSTANDART завоевал доверие автовладельцев как производитель доступных и надежных автозапчастей, сочетающий международные стандарты качества с адаптацией к местным условиям эксплуатации. История бренда насчитывает более 20 лет, начиная с организации собственных производственных линий в Тольятти в 2005 году, где и сегодня выпускается значительная часть продукции для автомобилей ВАЗ. Специализация AVTOSTANDART изначально фокусировалась на деталях для российских автомобилей, таких как пружины подвески, тормозные колодки, рулевые наконечники и фильтры, но сегодня ассортимент включает компоненты для иномарок, включая коммерческий транспорт Mercedes, Volkswagen и Ford.
Философия бренда строится на принципе «неубиваемости» в условиях реальных дорог. Продукция проектируется с учетом специфики эксплуатации в регионах с плохим покрытием, перепадами температур и высокой влажностью. Например, тормозные колодки AVTOSTANDART производятся по безасбестовой технологии, обеспечивающей эффективное и бесшумное торможение даже при перегрузках, а их состав оптимизирован для минимизации износа дисков. Такие решения проходят многоступенчатые испытания на полигонах и в лабораториях, включая тесты на холодоустойчивость, абразивный износ и термостойкость, что гарантирует соответствие стандартам ECE R-90 и ДСТУ.
Система контроля качества — ключевой актив бренда. Все заводы, включая зарубежные партнерские площадки, работают по единым стандартам ISO 9001, IATF и ISO/TS 16949, что подтверждено сертификатами. Технологический процесс включает входной контроль материалов, прессовку с точным соблюдением температурных режимов, рентгенографию металлоконструкций и финальные ресурсные тесты. Это исключает брак, но рынок столкнулся с проблемой подделок. Для защиты потребителя AVTOSTANDART внедрил многоуровневую систему идентификации: голографические наклейки, QR-коды для верификации на официальном сайте, микротиснение на упаковке и лазерную гравировку на деталях.
Продукция бренда рассчитана на разные сценарии использования. Для повседневной эксплуатации в городском цикле или на трассе подходят стандартные линии, демонстрирующие ресурс, превышающий гарантийный срок при своевременном ТО. Однако для экстремальных режимов — таких, как спортивная езда, постоянные перегрузки или работа в условиях бездорожья — инженеры рекомендуют премиальные серии с усиленными характеристиками. Отзывы клиентов подчеркивают оптимальное соотношение цены и качества, хотя некоторые негативные оценки связаны с установкой неоригинальных деталей или нарушением регламентов обслуживания.
АвтоАльянс — ваш надежный партнер в мире автозапчастей. Мы предлагаем обширный каталог продукции бренда — от тормозных систем до компонентов подвески — с гарантией подлинности и профессиональными консультациями по установке. Наши клиенты получают доступ к деталям, протестированным в реальных дорожных условиях, по конкурентным ценам и с гибкой системой скидок для оптовых заказов.
Ассортимент:
- Гидравлика
- Глушители
- ДВС
- Карданные валы
- Комплекты поршневых колец
- КПП
- Опоры
- Подвеска
- Радиаторы
- Рулевая система
- Стойки и амортизаторы
- Ступицы и подшипники колес
- Тормозная система
- Трансмиссия
- Усиленный ступичный узел
- Фильтры и прочее
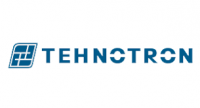
TEHNOTRON — созданное в Набережных Челнах передовое предприятие машиностроительной направленности, водящее в состав холдинга «ТЭМПО». Технотрон обеспечивает запчастями сферу коммерческой и сельскохозяйственной техники, в особенности электрооборудование, краны и почвообрабатывающую аппаратуру.
Располагая внушительной технической и научной базой в Набережных Челнах, Tehnotron независимо осуществляет полный цикл изготовления продукции, от проектирования и подготовки ресурсов, до тестирования и реализации товара, необходимого, в том числе для экономических нужд легкой и тяжелой промышленности.
Важно отметить, что в структурно-производственной цепи, есть место для проверки итогового продукта испытательным центром, который ответственен не только за предотвращение возможных проблем, но и за наиболее продуктивное совершенствование характеристик каждого конкретного изделия. Своим конкурентным преимуществом Технотрон выделяет особую технологию окрашивания автокомплектующих из SMC.
Бренд Tehnotron отвечает за соответствие высоким международным стандартам качества, что регулярно подтверждается обновляемым перечнем сертификатов и независимым органом оценки United Registrar of Systems Ltd. (URS Certification), благодаря контролю сырья, материалов и входящих комплектующих. Производственный потенциал в концерне позволяют конструировать и собирать все элементы самостоятельно в Набережных Челнах, не привлекая сторонние организации.
В настоящее время Технотрон в основном ориентированы на активное сотрудничество с такими автомобильными марками как ПАО «КАМАЗ», ОАО «МАЗ», «Группа ГАЗ», DAIMLER KAMAZ RUS и АЗ «УРАЛ». Компания стремится выйти на стабильный рост объемов производства, освоить также и региональные рынки и консолидировать автопромышленность.
Ассортимент:
- Система охлаждения
- Система питания
- Оперение кабины (экстерьер а/м 5490)
- Принадлежности кабины
- Элементы подвески
- Тягово-сцепные устройства
- Электрика
- Седельно-сцепные устройства
- Троллейный шинопровод и многое другое
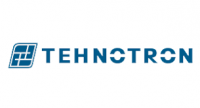
TEHNOTRON — созданное в Набережных Челнах передовое предприятие машиностроительной направленности, водящее в состав холдинга «ТЭМПО». Технотрон обеспечивает запчастями сферу коммерческой и сельскохозяйственной техники, в особенности электрооборудование, краны и почвообрабатывающую аппаратуру.
Располагая внушительной технической и научной базой в Набережных Челнах, Tehnotron независимо осуществляет полный цикл изготовления продукции, от проектирования и подготовки ресурсов, до тестирования и реализации товара, необходимого, в том числе для экономических нужд легкой и тяжелой промышленности.
Важно отметить, что в структурно-производственной цепи, есть место для проверки итогового продукта испытательным центром, который ответственен не только за предотвращение возможных проблем, но и за наиболее продуктивное совершенствование характеристик каждого конкретного изделия. Своим конкурентным преимуществом Технотрон выделяет особую технологию окрашивания автокомплектующих из SMC.
Бренд Tehnotron отвечает за соответствие высоким международным стандартам качества, что регулярно подтверждается обновляемым перечнем сертификатов и независимым органом оценки United Registrar of Systems Ltd. (URS Certification), благодаря контролю сырья, материалов и входящих комплектующих. Производственный потенциал в концерне позволяют конструировать и собирать все элементы самостоятельно в Набережных Челнах, не привлекая сторонние организации.
В настоящее время Технотрон в основном ориентированы на активное сотрудничество с такими автомобильными марками как ПАО «КАМАЗ», ОАО «МАЗ», «Группа ГАЗ», DAIMLER KAMAZ RUS и АЗ «УРАЛ». Компания стремится выйти на стабильный рост объемов производства, освоить также и региональные рынки и консолидировать автопромышленность.
Ассортимент:
- Система охлаждения
- Система питания
- Оперение кабины (экстерьер а/м 5490)
- Принадлежности кабины
- Элементы подвески
- Тягово-сцепные устройства
- Электрика
- Седельно-сцепные устройства
- Троллейный шинопровод и многое другое
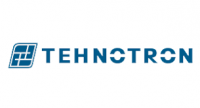
TEHNOTRON — созданное в Набережных Челнах передовое предприятие машиностроительной направленности, водящее в состав холдинга «ТЭМПО». Технотрон обеспечивает запчастями сферу коммерческой и сельскохозяйственной техники, в особенности электрооборудование, краны и почвообрабатывающую аппаратуру.
Располагая внушительной технической и научной базой в Набережных Челнах, Tehnotron независимо осуществляет полный цикл изготовления продукции, от проектирования и подготовки ресурсов, до тестирования и реализации товара, необходимого, в том числе для экономических нужд легкой и тяжелой промышленности.
Важно отметить, что в структурно-производственной цепи, есть место для проверки итогового продукта испытательным центром, который ответственен не только за предотвращение возможных проблем, но и за наиболее продуктивное совершенствование характеристик каждого конкретного изделия. Своим конкурентным преимуществом Технотрон выделяет особую технологию окрашивания автокомплектующих из SMC.
Бренд Tehnotron отвечает за соответствие высоким международным стандартам качества, что регулярно подтверждается обновляемым перечнем сертификатов и независимым органом оценки United Registrar of Systems Ltd. (URS Certification), благодаря контролю сырья, материалов и входящих комплектующих. Производственный потенциал в концерне позволяют конструировать и собирать все элементы самостоятельно в Набережных Челнах, не привлекая сторонние организации.
В настоящее время Технотрон в основном ориентированы на активное сотрудничество с такими автомобильными марками как ПАО «КАМАЗ», ОАО «МАЗ», «Группа ГАЗ», DAIMLER KAMAZ RUS и АЗ «УРАЛ». Компания стремится выйти на стабильный рост объемов производства, освоить также и региональные рынки и консолидировать автопромышленность.
Ассортимент:
- Система охлаждения
- Система питания
- Оперение кабины (экстерьер а/м 5490)
- Принадлежности кабины
- Элементы подвески
- Тягово-сцепные устройства
- Электрика
- Седельно-сцепные устройства
- Троллейный шинопровод и многое другое
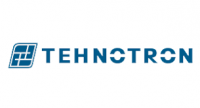
TEHNOTRON — созданное в Набережных Челнах передовое предприятие машиностроительной направленности, водящее в состав холдинга «ТЭМПО». Технотрон обеспечивает запчастями сферу коммерческой и сельскохозяйственной техники, в особенности электрооборудование, краны и почвообрабатывающую аппаратуру.
Располагая внушительной технической и научной базой в Набережных Челнах, Tehnotron независимо осуществляет полный цикл изготовления продукции, от проектирования и подготовки ресурсов, до тестирования и реализации товара, необходимого, в том числе для экономических нужд легкой и тяжелой промышленности.
Важно отметить, что в структурно-производственной цепи, есть место для проверки итогового продукта испытательным центром, который ответственен не только за предотвращение возможных проблем, но и за наиболее продуктивное совершенствование характеристик каждого конкретного изделия. Своим конкурентным преимуществом Технотрон выделяет особую технологию окрашивания автокомплектующих из SMC.
Бренд Tehnotron отвечает за соответствие высоким международным стандартам качества, что регулярно подтверждается обновляемым перечнем сертификатов и независимым органом оценки United Registrar of Systems Ltd. (URS Certification), благодаря контролю сырья, материалов и входящих комплектующих. Производственный потенциал в концерне позволяют конструировать и собирать все элементы самостоятельно в Набережных Челнах, не привлекая сторонние организации.
В настоящее время Технотрон в основном ориентированы на активное сотрудничество с такими автомобильными марками как ПАО «КАМАЗ», ОАО «МАЗ», «Группа ГАЗ», DAIMLER KAMAZ RUS и АЗ «УРАЛ». Компания стремится выйти на стабильный рост объемов производства, освоить также и региональные рынки и консолидировать автопромышленность.
Ассортимент:
- Система охлаждения
- Система питания
- Оперение кабины (экстерьер а/м 5490)
- Принадлежности кабины
- Элементы подвески
- Тягово-сцепные устройства
- Электрика
- Седельно-сцепные устройства
- Троллейный шинопровод и многое другое
На складах : 8345 шт.
На складах : 7102 шт.
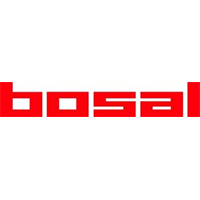
BOSAL - бренд, который является лидирующим в производстве выхлопных систем, катализаторов и автомобильных конвенторов. Компания BOSAL более ста лет считается одним из наиболее уважаемых брендов среди автолюбителей по всему миру.
Одним из главных преимуществ продукции BOSAL можно назвать её долговечность. Все детали проходят тщательный контроль качества перед тем, как попасть на конвейер. Это позволяет компании предоставлять гарантию на свою продукцию до 5 лет!
Важным фактором является экономия топлива благодаря оптимальной работе двигателя после установки запчастей от BOSAL. Системы выпуска изготавливаются из современных материалов с применением уникальных технологических решений, что сокращает уровень шума и уменьшает количество вредных выбросов.
При поиске автзапчастей для своего транспортного средства очень важно обращать внимание не только на цену, но и на качество сборки. В этом случае можно быть уверенным в том, что продукция BOSAL — это не только надежность, но и экономия на ремонте в долгосрочной перспективе.
Каждая деталь производится из высококачественного сырья с применением самых современных технологий. Катализаторы изготавливаются из металла, который обеспечивает быстрый разогрев двигателя. Материалы для выпускных систем имеют устойчивость к коррозии и гарантируют ей безупречную работу в течение многих лет.
Автозапчасти BOSAL отличается своей инновационностью: бренд постоянно разрабатывает новые технологии для создания более эффективных компонентов. Это дает автопроизводителям возможность использовать эти продукты для повышения экономичности и функциональности своих автомобилей.
Ключевым аспектом для BOSAL является удовлетворение даже самых сложных клиентских запросов. Это обеспечивается обширным каталогом предлагаемых товаров, в котором можно найти компоненты для различных автомобилей.
Ассортимент:
- Выхлопные системы
- Глушители
- Каталитические конверторы
- Катализаторы
- Крепежные элементы для выхлопных систем
- Клеммы для выхлопных систем
На складах : 28 шт.
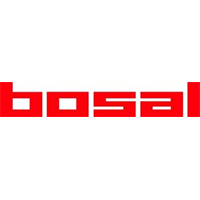
BOSAL - бренд, который является лидирующим в производстве выхлопных систем, катализаторов и автомобильных конвенторов. Компания BOSAL более ста лет считается одним из наиболее уважаемых брендов среди автолюбителей по всему миру.
Одним из главных преимуществ продукции BOSAL можно назвать её долговечность. Все детали проходят тщательный контроль качества перед тем, как попасть на конвейер. Это позволяет компании предоставлять гарантию на свою продукцию до 5 лет!
Важным фактором является экономия топлива благодаря оптимальной работе двигателя после установки запчастей от BOSAL. Системы выпуска изготавливаются из современных материалов с применением уникальных технологических решений, что сокращает уровень шума и уменьшает количество вредных выбросов.
При поиске автзапчастей для своего транспортного средства очень важно обращать внимание не только на цену, но и на качество сборки. В этом случае можно быть уверенным в том, что продукция BOSAL — это не только надежность, но и экономия на ремонте в долгосрочной перспективе.
Каждая деталь производится из высококачественного сырья с применением самых современных технологий. Катализаторы изготавливаются из металла, который обеспечивает быстрый разогрев двигателя. Материалы для выпускных систем имеют устойчивость к коррозии и гарантируют ей безупречную работу в течение многих лет.
Автозапчасти BOSAL отличается своей инновационностью: бренд постоянно разрабатывает новые технологии для создания более эффективных компонентов. Это дает автопроизводителям возможность использовать эти продукты для повышения экономичности и функциональности своих автомобилей.
Ключевым аспектом для BOSAL является удовлетворение даже самых сложных клиентских запросов. Это обеспечивается обширным каталогом предлагаемых товаров, в котором можно найти компоненты для различных автомобилей.
Ассортимент:
- Выхлопные системы
- Глушители
- Каталитические конверторы
- Катализаторы
- Крепежные элементы для выхлопных систем
- Клеммы для выхлопных систем
На складах : 21 шт.
На складах : 889 шт.
На складах : 722 шт.